Top Inventory Management Software for Manufacturing
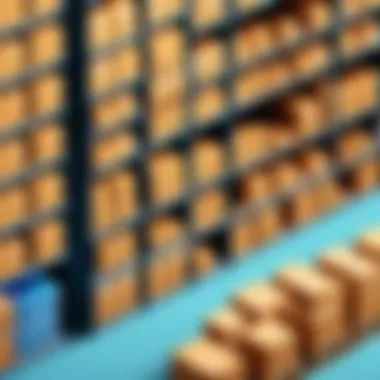
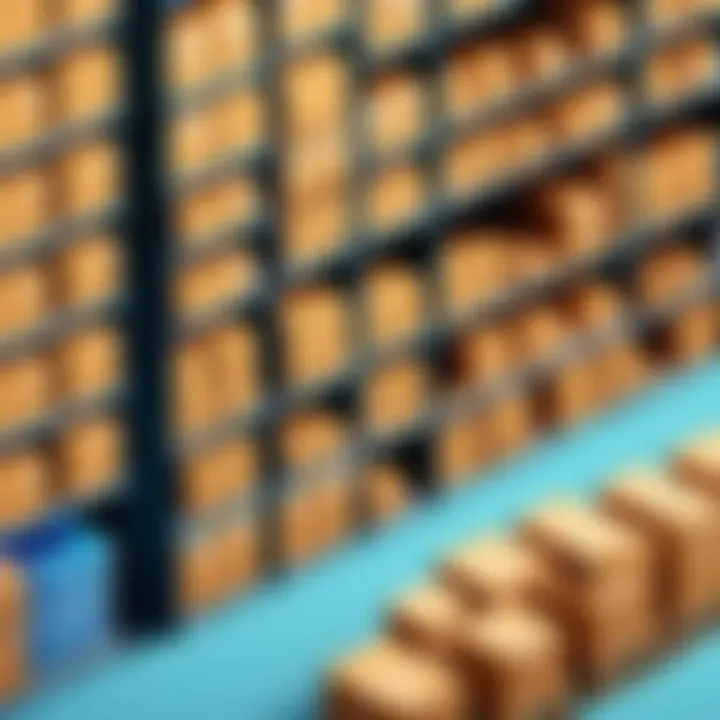
Intro
In the ever-evolving manufacturing landscape, efficient inventory management plays a pivotal role in ensuring a seamless production process. The need for precision and control over materials has never been greater. Various inventory management software solutions are available today tailored specifically for the manufacturing sector. This guide provides a deep dive into these solutions, offering comprehensive insights into their key features, advantages, and disadvantages.
By understanding the landscape, manufacturers can make informed decisions that align with their operational needs. The manufacturing process is not only about raw materials but also about the smooth flow of operations, reducing waste, and optimizing resources. To achieve this, having the right inventory management software is essential.
Key Features
Overview of Features
Modern inventory management software comes packed with a variety of essential features. These are designed to meet the unique demands of the manufacturing industry. Common features include:
- Real-Time Tracking: Continuous monitoring of inventory levels, allowing for timely reordering and replenishment.
- Reporting and Analytics: Comprehensive data analysis tools that provide insights into inventory turnover and stock levels.
- Integration Capabilities: This allows seamless connections with other systems like ERP, CRM, and supply chain management tools.
- User-Friendly Interface: A simple and intuitive UI enhances usability, making it easier for staff to adopt.
- Multi-Location Support: This caters to manufacturers with multiple warehouses or production sites, ensuring coherency across locations.
Unique Selling Points
Each software option has unique strengths that make it stand out in the crowded market. For example:
- Oracle NetSuite: Known for its comprehensive ERP functionalities alongside robust inventory management tools.
- Fishbowl: Offers advanced manufacturing integrations, particularly useful for businesses looking to streamline operations.
- inFlow Inventory: Delivers a straightforward approach with an emphasis on small to medium-sized manufacturers, focusing on ease of use.
Performance Evaluation
Speed and Responsiveness
The efficiency of an inventory management system is often dictated by its speed and responsiveness. Modern software should load quickly and process information in real time. This minimizes downtime and maximizes productivity. Users have noted variances in performance based on the underlying architecture of the software.
Resource Usage
Software must operate efficiently regarding resource usage. High-demand systems can drain resources, leading to sluggish performance. Evaluating a softwareโs need for CPU and memory is crucial. Many solutions now offer cloud-based options, which can reduce local resource strain and enhance accessibility.
In summary, a well-chosen inventory management software can significantly streamline operations and improve overall efficiency in manufacturing.
Being informed about the features and performance aspects will empower manufacturers to align their choices with specific operational strategies. Thus, the decision becomes less about brand preference and more about value addition to their business practices.
Understanding Inventory Management in Manufacturing
Inventory management stands as a critical discipline in the manufacturing sector. It encompasses a wide range of practices needed to ensure that products are available as needed while minimizing costs associated with holding and storing those products. Effective inventory management directly influences a manufacturerโs ability to serve customers, optimize operations, and maintain competitiveness in the marketplace.
Definition and Importance
Inventory management refers to the process of ordering, storing, and using a company's inventory. This inventory can include raw materials, work-in-progress products, and finished goods. The importance of inventory management cannot be overstated. It serves vital roles such as:
- Cost Control: Proper inventory management helps minimize costs associated with overstocking or stockouts.
- Operational Efficiency: Streamlined processes ensure resources are available when required, thus enhancing productivity.
- Customer Satisfaction: By maintaining the right levels of inventory, businesses can meet customer demand promptly, leading to improved satisfaction.
In a sector where margins can be thin and competition fierce, a robust inventory management strategy can mean the difference between a thriving business and one that struggles to survive. Organizations that grasp these elements can position themselves for long-term success.
Key Challenges in Manufacturing Inventory Management
Despite its significance, managing inventory in manufacturing comes with several challenges. Manufacturers face complexities not found in other sectors. Some of the notable challenges include:
- Demand Fluctuation: Demand for products can change rapidly due to market trends, which can lead to either excess inventory or shortages.
- Supply Chain Variability: Issues in the supply chain, such as delays from suppliers or transportation disruptions, can impact inventory levels and availability.
- Data Management: Maintaining accurate inventory data can be difficult, especially when using outdated systems or processes. Inaccurate data can lead to poor decision-making.
These challenges highlight the need for effective inventory management software. Such tools can help manufacturers tackle these issues by providing real-time insights, facilitating greater control over inventory levels, and boosting overall efficiency. As the market continues to evolve, understanding these challenges is the first step towards improving inventory management practices.
Core Features of Inventory Management Software
In the contemporary manufacturing landscape, the significance of robust inventory management cannot be overstated. Without the right tools, companies may face inefficiencies that could severely impact productivity and profit margins. Thus, understanding the core features of inventory management software is vital for any manufacturing firm aiming to streamline its operations. These features must not only address current needs but also predict future challenges as businesses evolve.

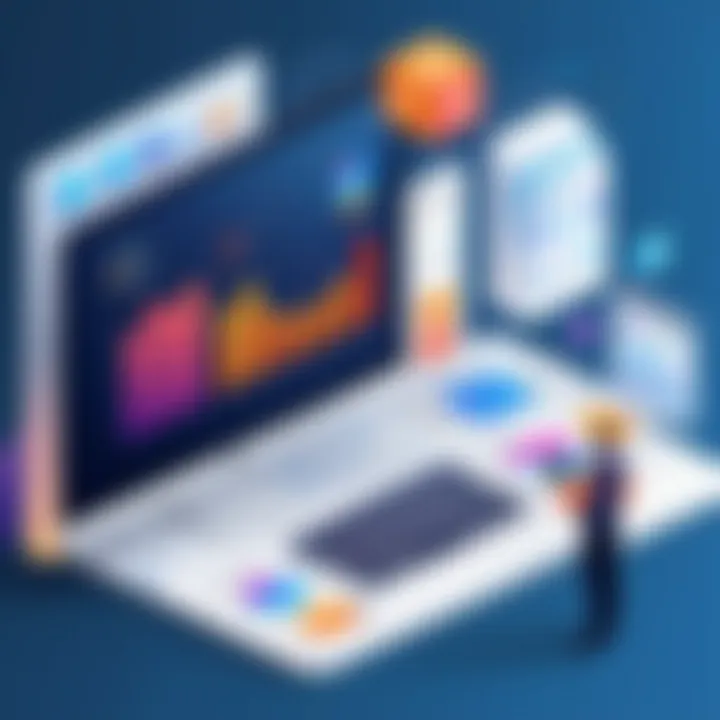
Real-Time Tracking and Reporting
One of the critical functionalities of inventory management software is real-time tracking and reporting. This feature allows manufacturers to oversee stock levels, order statuses, and inventory locations instantaneously. The advantage of real-time data is clear: it helps prevent stock shortages and overstock situations that can tie up capital unnecessarily.
Manufacturers can expect to see improved decision-making as a result of accurate reporting. For instance, access to up-to-date analytics can inform purchasing decisions and help with production scheduling. Moreover, this feature enables swift identification of discrepancies between physical and recorded stock levels, aiding in loss prevention. The ability to generate detailed reports on inventory performance boosts transparency within operations and can facilitate more informed strategic planning.
Automation of Inventory Processes
Another essential feature provided by advanced inventory management software is the automation of inventory processes. Automation minimizes the amount of manual input required, which can reduce human error and free up valuable time for employees. Processes such as reordering stock, tracking shipments, and managing inventory counts can all be handled automatically.
Benefits of automation extend beyond efficiency. For example, many software solutions utilize algorithms to predict demand patterns and initiate orders accordingly. This not only ensures that products are available when needed but also minimizes carrying costs. In the long term, this leads to improved cash flow management and cost savings, which are crucial for maintaining competitive advantage in manufacturing.
Integration with Other Systems
Lastly, the capacity for integration with other systems is a fundamental feature of effective inventory management software. Many businesses operate with diverse software solutions for accounting, sales, and production planning. A seamless integration ensures that data flows smoothly across all these platforms, creating a unified operational environment.
Effective integration leads to enhanced operational coherence and reduces the risk of data silos. For example, linking inventory management systems directly to sales platforms allows for real-time visibility into stock as it is sold. This immediacy can significantly improve responsiveness to market demands. Additionally, integration with finance systems can streamline budgeting and forecasting, assisting in maximizing profitability over time.
"The key to successful inventory management is not just in managing stock levels but integrating processes that lead to cohesive operations."
In summary, the core features of inventory management software play an essential role in enhancing productivity and efficiency within manufacturing operations. Real-time tracking, automation, and system integration collectively empower manufacturers to optimize their inventory processes significantly.
Evaluating Software Options
In today's dynamic manufacturing landscape, selecting the right inventory management software can significantly impact operational success. Evaluating software options is not just a task; it is a foundational step that ensures the chosen system aligns with the specific needs of your business. Given the wide array of features and tools available, manufacturers need to make informed decisions based on a thorough understanding of various elements. This section delves into key aspects like cost considerations, user experience, and customer support, which are critical in the evaluation process.
Cost Considerations
Cost is often a leading factor in software evaluation. Budget constraints can limit choices, yet it's essential to balance price with functionality. Consider both the initial investment and ongoing expenses, including maintenance, upgrades, and training. Some software solutions have tiered pricing models that accommodate different business scales.
- Initial Costs: Assess the buy-in price, which could include licensing fees, setup costs, and hardware if required.
- Ongoing Costs: Factor in subscription fees, and any additional modules that may incur extra charges after initial purchase.
- Hidden Costs: Look out for costs linked to customer support, updates, and unforeseen issues during implementation.
A comprehensive cost analysis can help organizations avoid unexpected financial burdens. Evaluate whether a higher upfront cost translates to better long-term savings due to improved efficiency or decreased errors.
User Interface and Experience
User interface and experience play a crucial role in software usability. An intuitive interface makes it easier for employees to adapt, reducing the time and resources spent on training. Well-designed inventory management systems should prioritize user engagement with functionalities that are easy to navigate. Look for the following:
- Clarity and Simplicity: The software should present data clearly, minimizing confusion and facilitating quicker decision-making.
- Customization Options: A solution that can be tailored to fit the specific workflows of a manufacturing company is often preferable.
- Accessibility: Ensure the software can be easily accessed across devices and platforms, allowing flexibility in operation.
Investing in a user-friendly interface can significantly heighten productivity, as employees are less likely to struggle with the systemโs navigation.
Customer Support and Community
Strong customer support is invaluable when implementing new software. Manufacturing environments can be fast-paced, necessitating timely assistance when issues arise. Evaluate the support channels that come with the software:
- Availability: Consider if support is offered 24/7 or only during business hours.
- Channels of Support: Identify the methods available, such as phone, chat, or email, to ensure help can be reached quickly.
- Community Resources: A vibrant user community can provide additional support that formal channels may not cover. Online forums, user groups, and documentation can be tremendously helpful.
"Effective customer support can enhance the operating experience of inventory management systems, leading to quicker resolutions and reduced downtime."
Emphasizing these aspects during your evaluation can establish a more sustainable and efficient inventory management system, ultimately benefiting your manufacturing operations.
Top Inventory Management Software for Manufacturing
Selecting the right inventory management software is crucial for manufacturers. This software streamlines processes, enhances visibility, and improves efficiency. It can aid in reducing costs by optimizing inventory levels and preventing stockouts. In a competitive industry like manufacturing, having an effective inventory management solution can set a company apart.
This section focuses on three leading software options that offer unique features tailored to manufacturing needs. By understanding the pros and cons of each, businesses can make informed decisions, which is essential for operational success.
Software A Overview
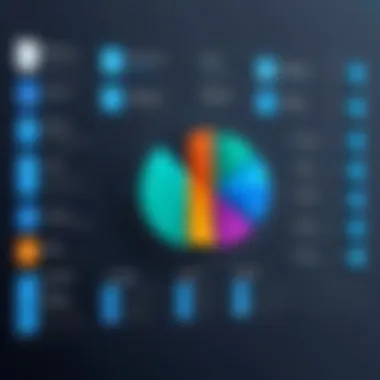
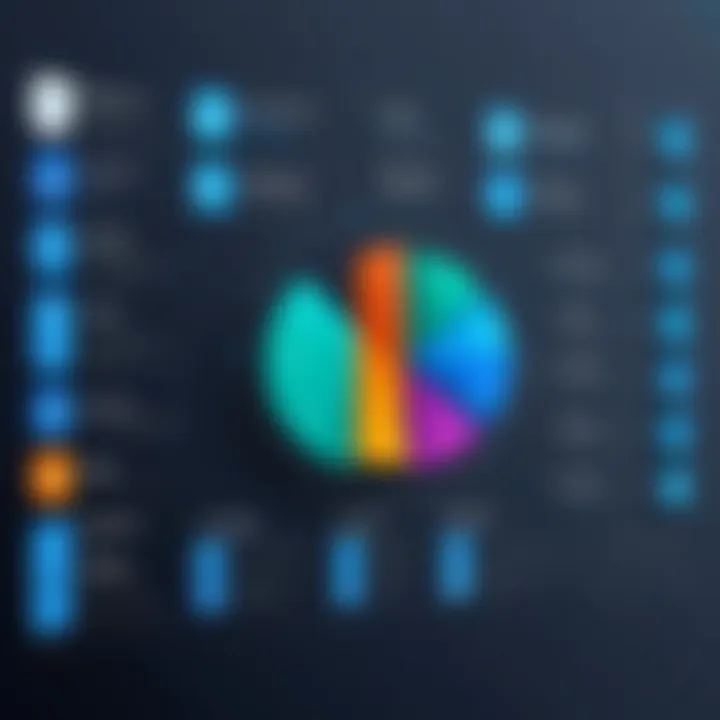
Key Features
Software A stands out for its robust tracking capabilities. It provides real-time data on stock levels, allowing manufacturers to make immediate adjustments. A notable characteristic of Software A is its user-friendly dashboard. This ease of use can significantly reduce the time spent on training staff and minimize errors.
Another unique feature of Software A is its demand forecasting tool. This assists manufacturers in predicting future inventory needs based on historical data. However, this tool may require accurate input data to function optimally, which can be a limitation for some users.
Pros and Cons
The strengths of Software A include its intuitive interface and comprehensive support resources. It is well-regarded in the industry, making it a popular choice among manufacturers. However, a drawback could be its subscription cost, which may be higher compared to competitors. Businesses must weigh the cost against the potential efficiency gains.
Pricing Structure
Software A follows a tiered pricing model. Each tier includes different features, making it essential for businesses to choose one that aligns with their needs. Higher-tier plans usually offer advanced features like automated reporting and detailed analytics, which can justify the increased expenses. Nonetheless, lower-tier plans may lack essential tools, leading to potential compromises.
Software B Overview
Key Features
Software B excels in automation features. Its automation of various inventory processes can save time and reduce human error. A significant strength of Software B is its integration capability with other systems like ERP and CRM platforms, which streamlines operations further. The seamless integration is a key reason many companies prefer this software.
On the downside, the automation features may require substantial initial setup time. Users need to customize workflows before fully benefiting from these capabilities.
Pros and Cons
The main advantages of Software B include increased efficiency due to automation and strong user feedback regarding its integration capabilities. However, some users report a steeper learning curve, which can delay the implementation process. Proper training is recommended to ensure that all users can leverage its full potential.
Pricing Structure
In terms of pricing, Software B offers flexible options tailored to different business scales. Smaller businesses may find the lower-priced tiers accommodating, while larger enterprises might gravitate toward the more comprehensive packages. The pricing structure promotes scalability, allowing firms to grow without needing a feared overhaul.
Software Overview
Key Features
Software C prides itself on its advanced analytics tools. These tools allow manufacturers to gain insights from inventory data, leading to better decision-making. One standout feature is the customizable reporting capability, enabling users to create reports aligned with their specific goals. This customization is a vital benefit for companies that rely heavily on data for ultimate growth.
However, the complexity of these tools may require dedicated training and support. Users might encounter difficulties if they do not have a clear understanding of the analytics features.
Pros and Cons
One of the strengths of Software C is its analytical depth, providing users with a competitive edge through informed decisions. The downside, however, is the potential overwhelm from too much data, which may lead to indecision or confusion without proper guidance.
Pricing Structure
Software C utilizes a subscription-based pricing model with options for annual and monthly payment plans. While the monthly option allows flexibility, the annual commitment tends to be cheaper in the long-run. Companies looking for extensive analytic features may find this a wise investment despite the initial costs.
Case Studies and Use Cases
Case studies and use cases are critical components in understanding the effectiveness of inventory management software in the manufacturing sector. By examining real-world examples, manufacturers can gain practical insights into how specific software solutions are implemented. This section demonstrates the concrete benefits and challenges businesses face when integrating these tools into their operations.
Manufacturing Company A
Implementation Process
The implementation process of Manufacturing Company A involved a comprehensive assessment of existing inventory practices. This initial phase allowed the team to identify gaps and inefficiencies. A distinctive aspect of their approach was the involvement of cross-functional teams, which ensured that different perspectives were taken into account during implementation.
By prioritizing user training, the company capitalized on the software's capabilities, ensuring all staff members were proficient. This characteristic of inclusion during the implementation stage not only streamlined processes but also created ownership among employees towards the new system. However, a challenge faced was resistance to change from long-term employees, which slowed adoption in the early stages.

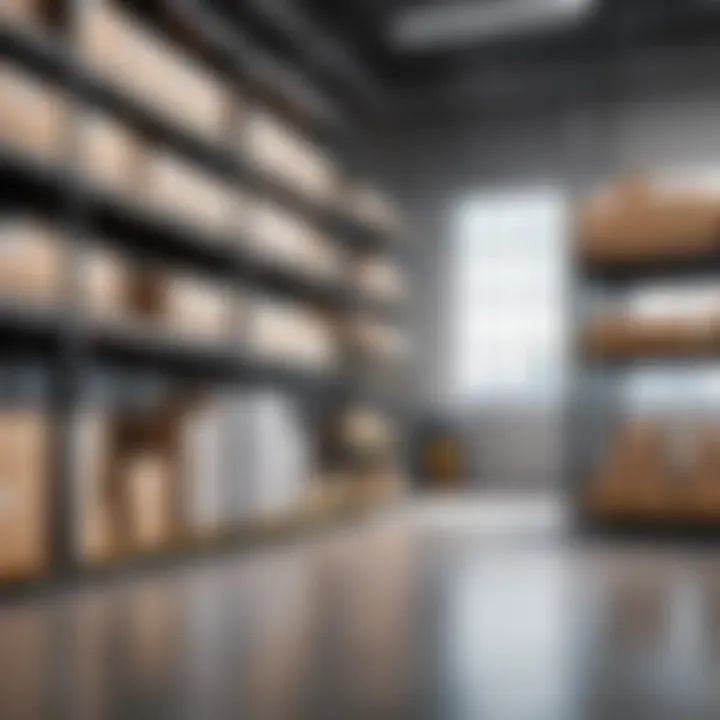
Results Achieved
As a result of the system's implementation, Manufacturing Company A noted a significant reduction in inventory discrepancies. The key characteristics of this success included enhanced visibility into stock levels and improved reporting accuracy. By facilitating real-time data access, managers could make informed decisions promptly.
A unique feature was the integration of automated reorder systems, which minimized stockouts. While this has been beneficial, some drawbacks included reliance on the software's analytics, which occasionally produced less accurate forecasts due to data entry errors.
Manufacturing Company B
Implementation Process
Manufacturing Company B's implementation process highlighted a phased approach to minimize disruption. This step-by-step rollout allowed each department to adapt without overwhelming the staff. A notable characteristic of their strategy was effective communication throughout the organization regarding the benefits of the new software.
One unique feature of this process was the pilot program, where inventory management software was tested in a single department before full-scale deployment. This cautious approach proved beneficial as it allowed adjustments based on feedback and performance metrics. However, it also required more time than anticipated, presenting a challenge to meet timelines.
Results Achieved
Once the software was fully implemented, Manufacturing Company B experienced streamlined operations and an evident decrease in carrying costs. The key benefit of achieving such results was the increase in inventory turnover rates, which improved cash flow for the company.
The unique feature here was the ability to analyze historical data for better forecasting. However, a potential disadvantage to note was the learning curve faced by employees, which temporarily slowed down processes in the early days after full implementation.
Case studies reveal that the real-world impact of inventory management software often varies based on implementation strategies, highlighting the importance of tailoring approaches to each organization's unique needs.
By examining these case studies, manufacturers can glean lessons that inform their decisions about which inventory management software to choose and how to navigate its implementation.
Future Trends in Inventory Management Software
In today's rapidly evolving manufacturing landscape, inventory management software must adapt to new technologies and methodologies. Understanding the future trends is crucial for businesses that want to stay competitive. This section discusses emerging trends in inventory management software that will shape the way manufacturers operate.
Artificial Intelligence and Machine Learning
Artificial Intelligence (AI) and Machine Learning (ML) are becoming integral components of inventory management systems. They enhance decision-making processes by analyzing vast amounts of data to offer insights that human planners might miss. These technologies can predict demand fluctuations, suggest optimal stock levels, and even automate the reordering process.
The adoption of AI and ML can lead to significant cost savings. For instance, manufacturers can reduce excess inventory and minimize stockouts.
Benefits of AI and ML in inventory management include:
- Forecast Accuracy: By processing historical data, these technologies improve the precision of demand forecasts.
- Operational Efficiency: Automated workflows reduce manual effort, speeding up inventory tasks.
- Data-Driven Insights: AI algorithms identify trends and suggest actions based on real-time data.
Challenges to consider include the initial cost of integration and the need for training staff to utilize these technologies effectively.
"AI in inventory management not only streamlines processes but also provides profound insights that redefine operational strategies."
Cloud-Based Solutions
Cloud-based inventory management solutions are transforming how manufacturers manage their assets. These systems offer accessibility, scalability, and flexibility, allowing teams to operate from various locations without the constraints of physical infrastructure. Using cloud technology ensures real-time data synchronization across the organization.
Key advantages of cloud-based solutions include:
- Cost Efficiency: Minimal upfront investment is required compared to traditional systems.
- Remote Access: Stakeholders can access inventory data and perform tasks from anywhere, improving responsiveness.
- Integration Capabilities: Cloud solutions often integrate seamlessly with other such as ERP and CRM systems, ensuring a streamlined workflow.
There are, however, considerations for cloud service selection. Security of sensitive data and the reliability of internet access are paramount. As the landscape evolves, manufacturers must stay abreast of these trends to optimize their inventory management practices.
Epilogue
In this article, we have explored the complex landscape of inventory management software specifically designed for the manufacturing sector. The significance of this topic cannot be overstated. Effective inventory management is the backbone of successful manufacturing operations. It impacts production lines, cost efficiency, and ultimately, customer satisfaction.
Summary of Key Points
Throughout this guide, we discussed various key elements that contribute to effective inventory management. We emphasized the importance of features such as real-time tracking, automation, and system integration. These capabilities enable manufacturers to maintain optimal inventory levels, thereby reducing excess stock and minimizing costs.
We also evaluated several software options available in the market, highlighting their unique features, advantages, and potential drawbacks. By incorporating case studies, we illustrated how different companies have successfully implemented these technologies to improve their operations.
Final Recommendations
When selecting an inventory management software, it is crucial to consider both current and future needs. Focus on the software's scalability, its ability to integrate with existing systems, and whether it can adapt to specific manufacturing processes. In addition, always assess the cost versus the benefits each software brings.